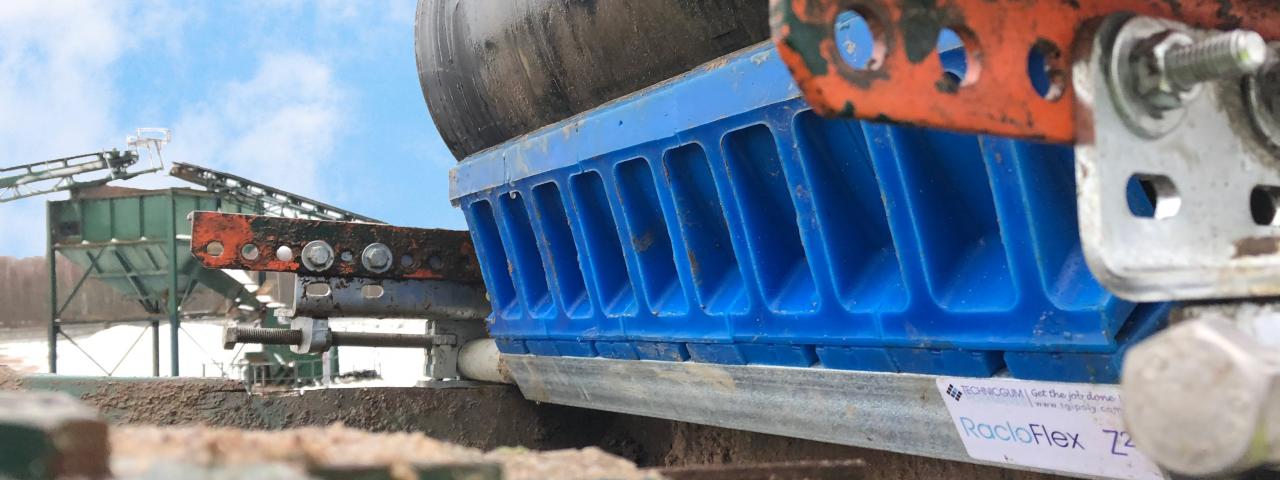
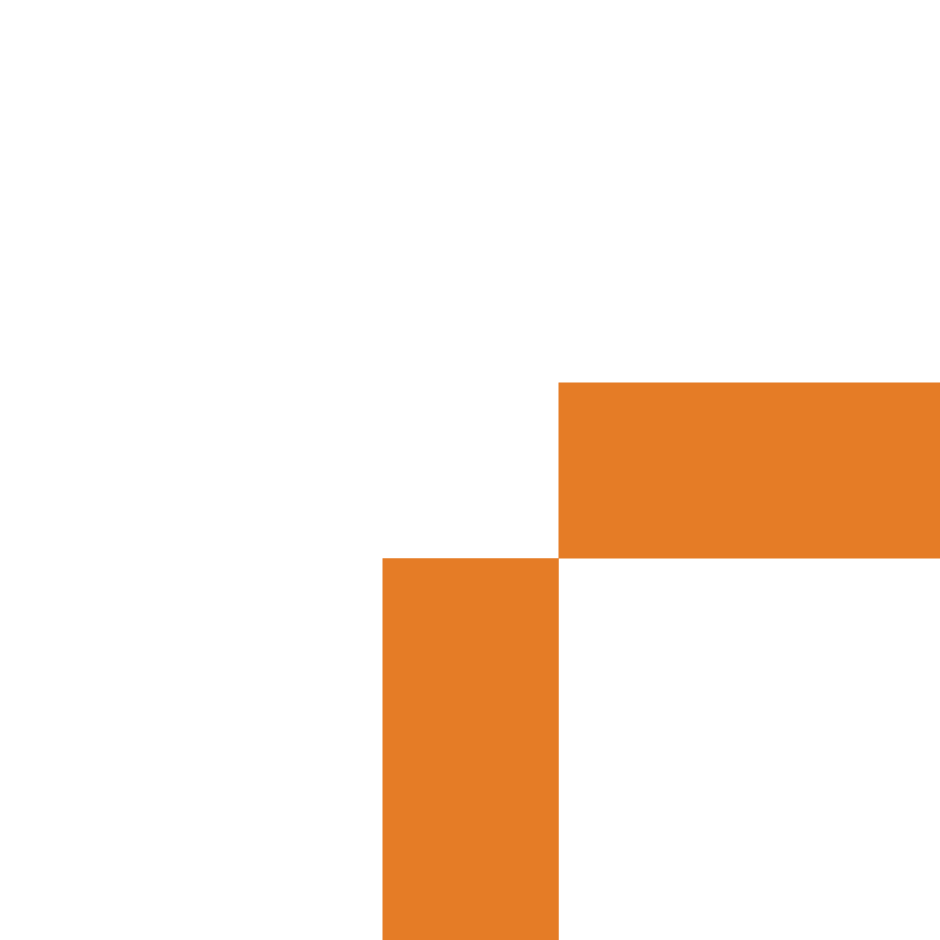
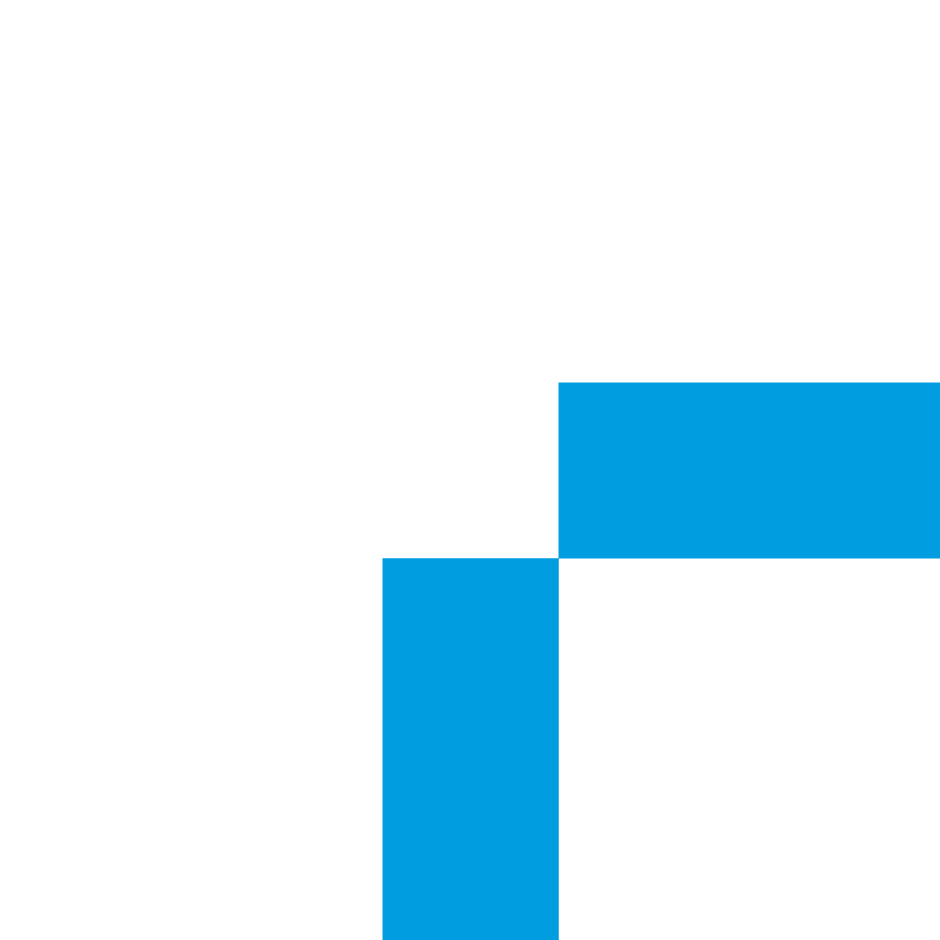
Conveyor belt cleaning
Conveyor belt cleaners are essential equipment for your conveyors.
You might have noticed carryback on your conveyor belts, and you wonder how to keep them clean?
Are you tired of your belts getting damaged way too fast? This is where conveyor belt cleaning comes in.
Conveyor belt cleaning systems such as belt cleaners and scrapers will save you the trouble of frequent belt cleaning while increasing your conveyor's productivity.
Your staff will be available to perform other tasks and remain safe.
MLT's conveyor belt cleaning solutions work with all belt sizes or speeds no matter the environment or industry (mines, fertilizer and chemical, foundries and steel mills, ports...)
RacloFlex™ Z² HD
A multi-blade primary scraper unique on the market. A system compatible with SUPER‑SCREW®*, ISC™ & FIX'N GO®
An ingenious conveyor belt cleaning system that fits most conveyor structures. Each anti-clogging profile blade is equipped with internal 2 springs and is quickly connected on a pivot that allows slight rotation and easy change without adjustment. The…
RacloFlex™ SW
A unique and innovative scraper, The only one with wear compensation
An ingenious scraping system that adapts to your belt. The RacloFlex™ SW has a blade with two inserts that transfer the lateral external pressures to an increased central pressure. Therefore, the scraper adapts automatically and compensates for its wear continuously…
RacloFlex™ Metal
Maximum efficiency : economical maintenance
Independent replacement and adjustment of each blade. Due to the natural slope of the substance carried, the cleaning is intense in the center of the belt and causes a faster wear of the scraper. A simple mono-blade scraper cannot correct this problem and its blade must be changed…
RacloFlex™ N
Structure protected for a long time
An ingenious and adaptable conveyor belt cleaning system. Unlike the simple single-blade scrapers, the RacloFlex™ N is composed of blades each supported by a shock absorber block which can be adjusted independently to shape the belt and compensate for the faster wear of certain blades…
RacloFlex™ NT
An innovation that prevents wear and tear
Ingenious conveyor belt cleaning equipment that compensates for wear. Unlike the simple single-blade scrapers, the RacloFlex™ NT is composed of blades each supported by a shock absorber block which can be adjusted independently to shape the belt and compensate to the faster wear…
RacloFlex™ VP
Pilot segmented scraper with automatic pressure, high performance system and optimised service life
An articulated system that adapts to dangerous situations. The articulated parallelogram support keeps permanent contact with the belt no matter the wear level of the blade and makes it possible to raise it in case of danger. Compatible with SUPER‑SCREW®*, ISC™,…
RacloFlex™ DP
Technical, reliable and robust solution
Adjustable conveyor belt cleaning solution, permanent contact with the belt. The sliding support allows a movement up and down of the complete structure so the cleaner keeps permanent contact with the belt regardless of the level of wear of the blade and allows it to rise in dangerous situations. The blade is made of…
Benefits of effective conveyor belt cleaning
Description G
Implementing effective conveyor belt cleaning provides major benefits, including:
• Eliminating carryback: conveyor belt cleaning equipment greatly reduces the accumulation of material and dust during and between conveying operations and helps prevent carryback.
• Extending equipment lifespan: carryback often accumulates under the belt and inside the conveyor system, potentially damaging components like rollers and idlers and causing belts to wander and fray. Keeping belts clean helps prevent premature damage and extends the longevity of conveyor equipment.
• Reducing energy consumption: accumulating material beyond the head pulley creates additional weight and forces the system to work harder, increasing energy use. Thus, maintaining a clean belt results in lower energy costs.
• Minimizing material loss and spillage: limiting carryback and dust positively impacts transfer point and sealing from conveyor belt systems, therefore reducing risks of product spillage and/or loss.
• Increasing profitability: minimizing or eliminating carryback leads to lower clean-up, maintenance, and energy expenses and enhances overall profitability.
• Improving workplace safety: accumulating fugitive material and dust under the belt can create slippery surfaces, leading workers to slip or fall and become safety hazards if inhaled or ignited. Minimizing those elements creates a safer work environment for employees.
Conveyor belt cleaning solutions
Description D
At MLT Group, we offer multiple solutions to efficiently clean belts, prevent carryback, and ensure the safety and efficiency of your conveyor belt system. Our conveyor belt cleaning equipment is adapted to all belt sizes, speeds, industries, and environments.
Whether you are looking for conveyor belt scrapers, or primary or secondary cleaners, from multi-blade primary cleaners to compensatory or internal cleaners, find the solution best suited to your needs among our choice of high-performing conveyor belt cleaning systems!
Primary cleaners
MLT’s RacloFlex™ Z² and RacloFlex™ NT primary belt cleaners are both ingenious systems meant to be mounted to the head pulley and capable of removing large pieces of material off conveyor belts. They are available in a variety of scraping widths and number of blades.
Secondary cleaners
MLT offers several choices of secondary belt cleaners. The RacloFlex™ N is a safe value and a rational solution for conveyor belt cleaning, while the RacloFlex™ SW guarantees maximum efficiency and lifetime with minimum maintenance. They can both be used to remove remaining material on conveyor belts beyond the head pulley. They are available in many scraping widths and number of blades.
Internal cleaners
Our range of conveyor belt cleaning solutions also includes an articulated belt cleaner (the RacloFlex™ VP) as well as an adjustable belt cleaner (the RacloFlex™ DP) would you require equipments for the internal cleaning of your conveyor belt system.
Chosing the right conveyor belt cleaner
Content
Selecting the optimal conveyor belt cleaning solution requires a clear understanding of your system’s operational needs, the type of materials being handled, and specific conditions that can impact cleaning effectiveness. Here are a few factors to chose the right belt cleaner:
Type of material transported
The nature of the material carried by the conveyor greatly influences the choice of cleaner. For instance:
- Sticky or high-moisture materials (such as clay, coal, or wet grains) may require multiple cleaning systems, such as primary and secondary cleaners, to effectively remove residue.
- Abrasive materials (such as sand or gravel) are best handled with durable, low-wear blade materials to ensure longevity.
- Fine particles often require brush-style cleaners or specialized secondary cleaners to remove minute debris that other cleaners might miss.
Conveyor belt speed and width
High-speed conveyors place more stress on belt cleaners, demanding robust materials and well-placed cleaner assemblies. In this way, faster-moving belts might require high-performance polyurethane blades to resist wear and reduce the need for frequent replacement. Wider belts may benefit from multiple cleaner installations across their width to ensure even coverage and maximum cleaning efficiency.
Maintenance frequency and accessibility
Accessibility is key, as cleaners will need routine checks and maintenance to function effectively. For systems with frequent servicing requirements, consider easily accessible blade replacement options. Opt for self-adjusting or low-maintenance cleaners in the case of remote or hard-to-access conveyors, as they reduce manual adjustments and save time on routine maintenance.
Do not hesitate to reach out to our technical team if you have a specific request or would like support in selecting the solution best suited for your application.