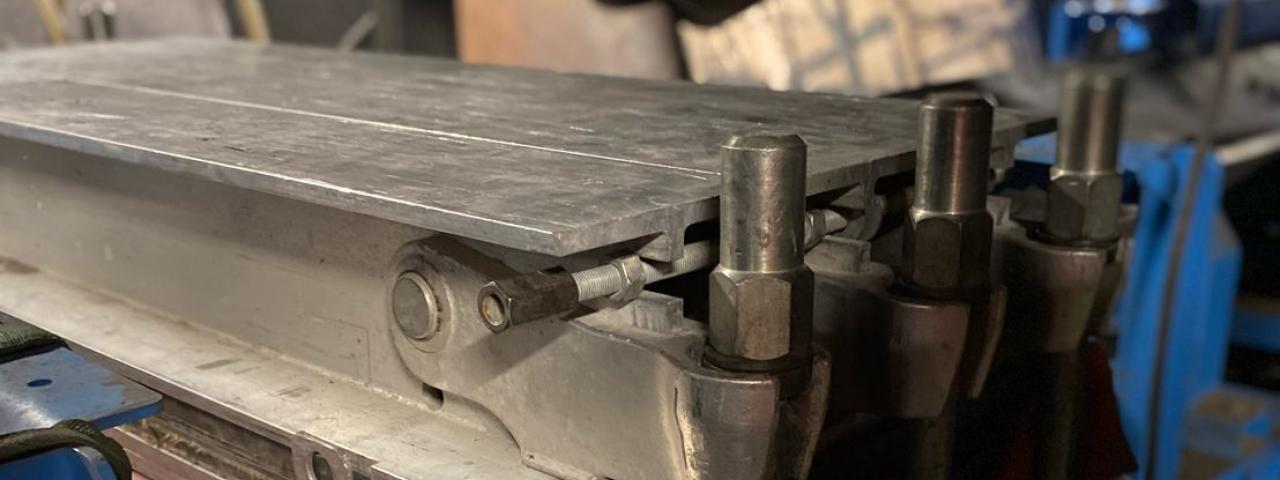
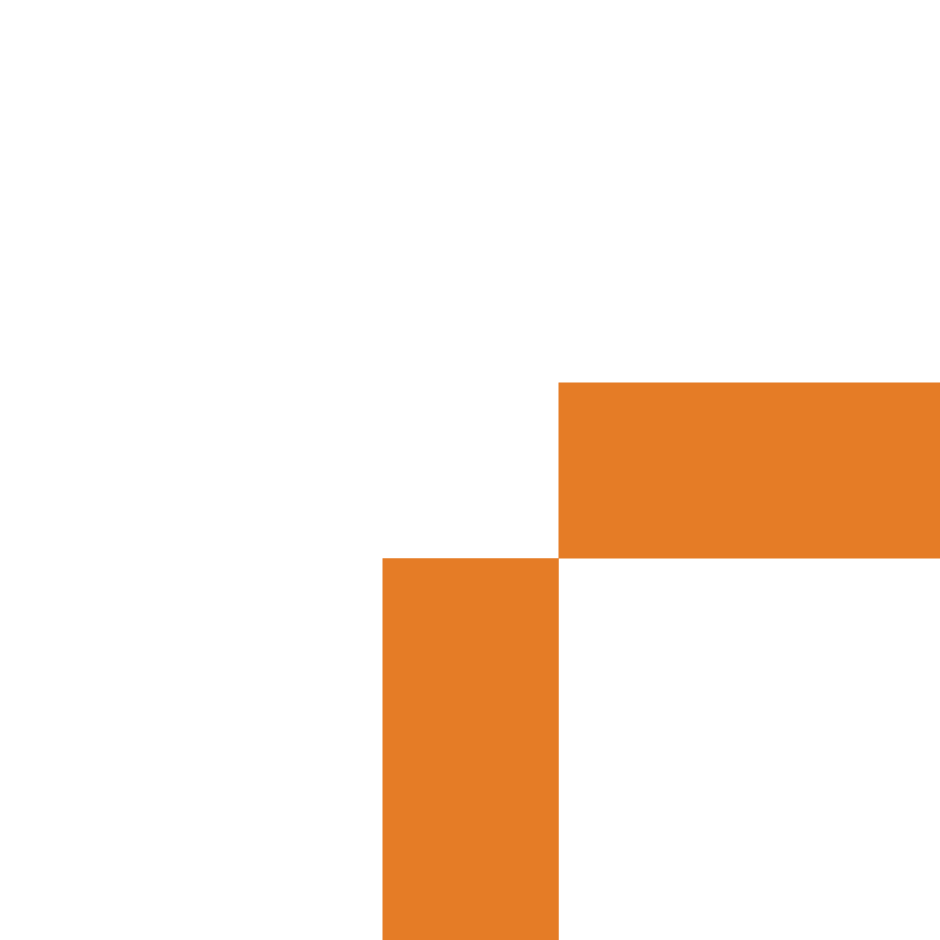
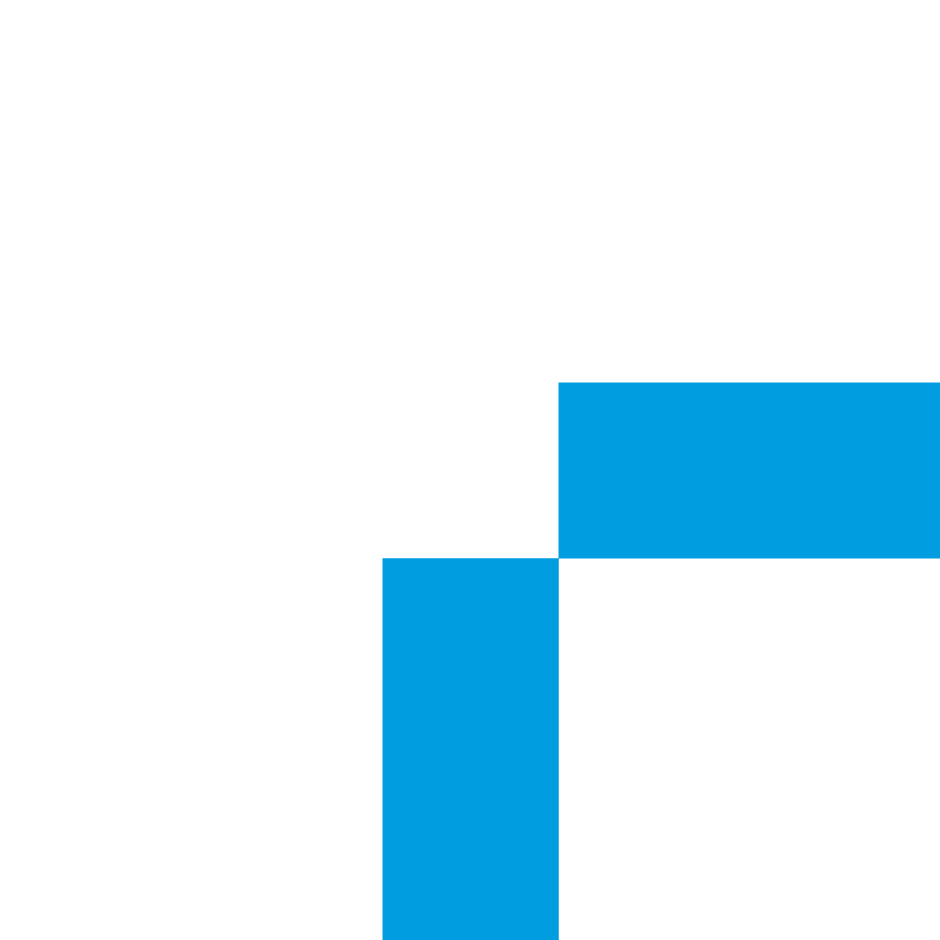
A Guide to Conveyor Belt Hot Vulcanizing
In the demanding field of continuous material handling, the reliability of conveyor belts is a strategic concern. When a conveyor belt breaks or requires splicing, operators have several methods available to them. One of these methods is hot vulcanization, a traditional technique that has been widely utilized in high-intensity industrial environments, including mining and quarrying. This guide offers a comprehensive overview of hot vulcanization, including its advantages and disadvantages, as well as modern alternatives that are available.
WHAT IS CONVEYOR BELT HOT VULCANIZING?
Conveyor belt hot vulcanizing is a process that permanently splices the two ends of a conveyor belt. It requires heating the belt ends to a high temperature, typically between 140°C and 160°C, while applying pressure. During this process, layers of raw rubber and reinforcing materials are added. This method recreates an almost seamless connection, both mechanically and in terms of sealing. After hot vulcanization, the result is a permanent splice that is resistant to wear, impact, and harsh environments. This ensures a perfect seal, which is essential for industries such as mining, cement, and food processing.
HOW TO VULCANIZE A CONVEYOR BELT?
CONVEYOR BELT VULCANIZING PROCEDURE
Proper vulcanization follows a step-by-step process. Below, is an outline of the standard procedure:
Step 1: Preparing the Belt Ends
Begin by carefully preparing the belt ends. This involves cutting them in a stepped or finger configuration, depending on the type of splice required. Additionally, the belt surface must be thoroughly cleaned to remove any contaminants such as dust, oil, or moisture.
Step 2: Applying the Vulcanizing Materials
Next, apply a layer of uncured rubber compound and vulcanizing cement to the prepared belt ends. These materials are essential for creating a strong bond during the curing process.
Step 3: Applying Heat and Pressure
The ends of the belt are placed in a vulcanizing press, where controlled heat and pressure are applied to start the chemical bonding process. The temperature and duration of this stage depend on the type of belt material and the vulcanizing agent used.
Step 4: Cooling and Curing
After the heat cycle is complete, the belt is allowed to cool gradually to ensure proper curing of the splice. It is important to note that removing the belt from the press too soon can weaken the bond and compromise the integrity of the splice.
Step 5: Inspection and Testing
Lastly, the splice must be thoroughly inspected for any defects, such as air bubbles or weak spots. A tension test may also be performed to verify the strength of the bond before the belt is returned to operation.
MOST COMMONLY USED VULCANIZING AGENTS & ADHESIVES
The effectiveness of vulcanization largely depends on the quality of the agents and adhesives utilized. Some of the most commonly used materials include:
- Uncured rubber: This is used as an interlayer between belt ends and fuses with the belt material when exposed to heat and pressure.
- Vulcanizing cement: This bonding agent enhances adhesion between the layers of the belt.
- Sulfur-based curing agents: These agents facilitate the chemical cross-linking process, which strengthens the bond/
HOW LONG DOES IT TAKE TO VULCANIZE A CONVEYOR BELT?
The time required to vulcanize a conveyor belt varies depending on the belt's thickness, material type, and environmental conditions. On average, the process takes anywhere from 45 minutes to several hours. It is important to also consider the cooling and curing times before the belt can be put back into service. Vulcanization generally requires more downtime than mechanical splicing.
ADVANTAGES OF HOT VULCANIZING A CONVEYOR BELT
Vulcanization presents several benefits compared to other methods of splicing conveyor belts, including:
- Enhanced Strength and Durability: Vulcanized belts retain their original tensile strength, resulting in a seamless and robust splice that can endure high loads and stress.
- Reduced Maintenance and Downtime: Unlike mechanical fasteners, which can loosen or break over time, the vulcanized section of the belt remains intact, minimizing the need for frequent maintenance and repairs
- Improved Belt Performance: This technique significantly lowers the risk of material catching on the splice, reducing the chances of spillage and enhancing the overall efficiency of material transfer.
- Increased Resistance to Wear and Tear: Vulcanized conveyor belts are highly resistant to harsh environmental factors such as heat, moisture, and abrasive materials, making them suitable for tough working conditions.
- Cost-Effective in the Long Run: While vulcanization requires a higher initial investment, its extended lifespan and lower maintenance costs make it a more economical choice over time.
CONSTRAINTS OF HOT VULCANIZING A CONVEYOR BELT
- Downtime : Long (4 to 8 hours)
- Requirements : Stable ambient temperature, clean, dry site
- Equipment : Press, generator, compressor, specialized tooling
- Workforce : Highly skilled
- Cost : High (labor + downtime + logistics)
SUPER-SCREW®: A STRATEGIC ALTERNATIVE TO CONVEYOR BELT VULCANIZATION
At MLT, we've designed the Super-Screw® splice to meet the needs of industrial sites that can't afford long production stoppages or operate in harsh conditions.
Key benefits:
- Fast installation: in less than 2 hours, without presses or heat.
- On-site intervention: even in wet, dusty or high conditions.
- High mechanical strength: up to 2500 N/mm depending on model.
- Suitable for splicing textile belts and repairing metal belts.
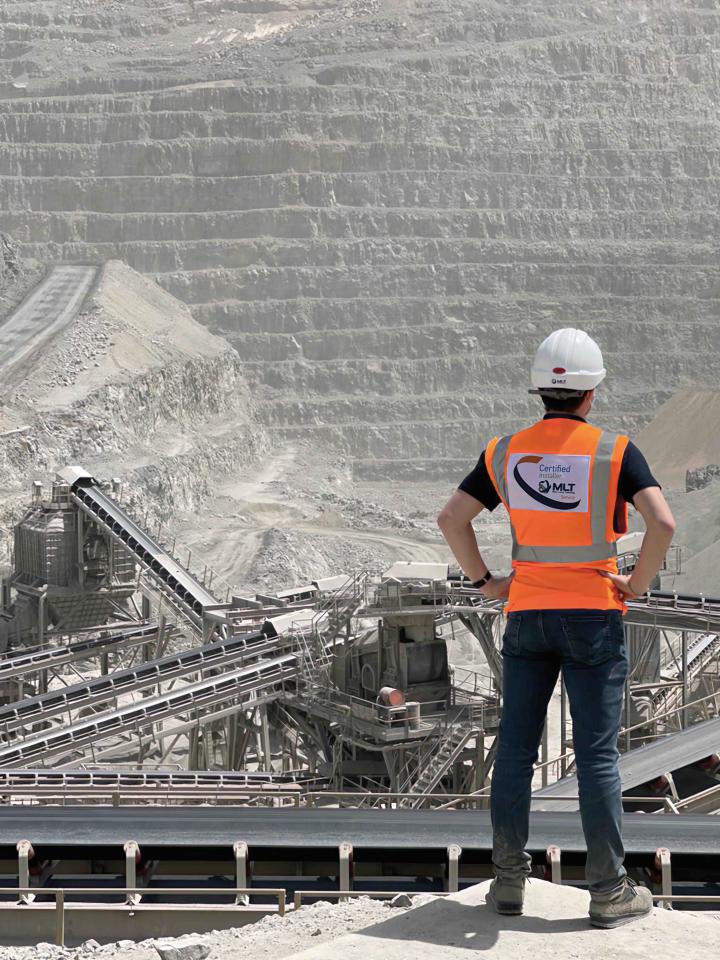
Content
Hot vulcanizing is a reliable and established method for permanently splicing conveyor belts. However, it comes with considerable challenges, including time constraints, logistical issues, and the need for specialized skills.
MLT offers a high-performance alternative with the Super-Screw® solution, which is designed to meet the practical needs of manufacturers. It provides a fast and dependable option for conveyor belt splicing.
If you would like to learn more about the Super-Screw® solution or need personalized assistance, please contact our MLT experts today.